Processing zinc alloy die-casting molds includes not only the processing of shearing dies and die-cutting dies, but also the processing of tools used for forming and blanking. In most cases, the mold will have an upper mold as well as a lower mold. The steel plate is positioned so that it is sandwiched between the upper and lower molds before the material is subjected to the press and given its final shape. When the press is opened, either the workpiece whose shape was determined by the mold will be obtained, or the waste material that corresponds to the shape of the mold will be removed. Molds can be used to form objects with dimensions as fine as electronic connectors and as large as automobile dashboards.
Die-casting method using zinc alloy molds as the processing medium
Materials for cutting include material for the front mold, material for the rear mold, Surface Finish Services material for the insert, material for the row position, and material for the inclined roof;The open frame includes the front mold frame and the rear mold frame;
Roughening: the front mold cavity, the rear mold cavity, and the parting line are all thickened; Roughening: the parting line is also thickened.
Copper male: front mold copper male, rear mold copper male, parting line clear angle copper male; Copper female: front mold copper female, rear mold copper female;
Insert the parting line, copper pin, and top pillow position in an inclined orientation for wire cutting;
Fine gong parting line and fine gong rear mold core are featured on the computer gong.
EDM: The front mold is thick and copper male, and the male mold line is clear in the corner. The rear mold is in the bone position and the pillow position.
Drilling, pinholes, and ejector pins; mold ejector pin holes, waterway hole processing positions, and position pressing; drilling, pinholes, and ejector pins
Flat top, compound thimble, and matching thimble; Inclined top.
There is a requirement for a high level of processing accuracy. A zinc alloy die-casting mold is typically made up of three distinct mold components: a concave mold, a punch mold, and a mold base. It's possible that some of them are multi-piece modules. Therefore, high levels of processing accuracy are required for the combination of upper and lower molds, the combination of inserts and cavities, and the joining together of modules. Precision molds typically achieve a level of dimensional accuracy that is measured in micrometers.
Some products with complicated shapes and surfaces, such as automobile panels, aircraft parts, toys, and home appliances, have a surface that is composed of a number of different curved surfaces in varying degrees of curvature. As a result, the cavity surface of the die-casting mold for zinc alloy is extremely complicated. Mathematical analysis is required for the treatment of some surfaces. The production of molds in small batches is not the same as production in mass quantities, and in many instances, only a single batch is made.
The production of multi-process molds always employs a variety of processes, including milling, boring, drilling, reaming, and tapping, among others. There is a finite amount of time that can be spent using molds for repetitive production. Because a mold needs to be replaced with a new one when it reaches the end of its service life, the production of molds is frequently iterative. In the production of molds using profiling processing, there are times when neither drawings nor data are available. In these cases, the profiling processing has to be carried out based on the actual object. For this purpose, high imitation accuracy die casting products and the absence of deformation are required.
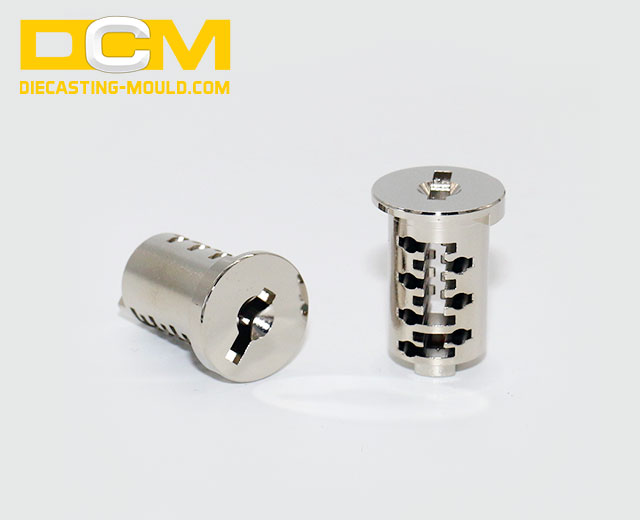
The materials used to make molds are of superior quality and have a high degree of tenacity. The high-quality alloy steel is typically used in the construction of molds as the primary material. Ledeburite steels, such as Crl2 and CrWMn, are frequently used in CNC machining the production of molds, particularly those with a long service life. When it comes to blank forging, processing, and heat treatment, this particular type of steel has very specific requirements. As a result, one cannot ignore the preparation of the processing technology, and heat treatment deformation is also a problem that needs to be taken seriously during the processing stage.
Prior to semi-finishing, the side datum plane is aligned to ensure accuracy; semi-finishing 2D and 3D profiles, and finishing various installation working surfaces (including limit block mounting surface and contact surface, insert mounting surface and backrest surface, punching surface), Head mounting surface, waste cutter mounting surface and backrest surface, spring mounting surface and contact surface, various stroke limit working surfaces, wedge mounting surface and baComplete the height reference surface as well as the process reference hole, and then record the data.
Before finishing, alignment of the process reference hole datum plane and insert allowance inspection; finishing profile 2D, 3D, side punching profile and hole location; finishing process reference hole and Height reference; finishing guide surface and guide hole. Inspection and review of the machining accuracy, bench work, and inlay process. The process should be prepared succinctly and expressed in detail, and the processing content should be expressed numerically as much as possible; the process should place particular emphasis on key and difficult processing points; the process should be clearly expressed where combined processing is required; when the insert needs to be processed separately, attention should be paid to the process requirements for processing accuracy; and the process should be carried out in the following order: 1. mix and match. After processing, for the insert parts that need to be processed separately, the process installation is the benchmark requirement for separate processing while combined processing is taking place; springs are the most easily damaged in zinc alloy die-casting mold processing, so mold springs with a long fatigue life should be selected.
Die-casting method using zinc alloy molds as the processing medium
Materials for cutting include material for the front mold, material for the rear mold, Surface Finish Services material for the insert, material for the row position, and material for the inclined roof;The open frame includes the front mold frame and the rear mold frame;
Roughening: the front mold cavity, the rear mold cavity, and the parting line are all thickened; Roughening: the parting line is also thickened.
Copper male: front mold copper male, rear mold copper male, parting line clear angle copper male; Copper female: front mold copper female, rear mold copper female;
Insert the parting line, copper pin, and top pillow position in an inclined orientation for wire cutting;
Fine gong parting line and fine gong rear mold core are featured on the computer gong.
EDM: The front mold is thick and copper male, and the male mold line is clear in the corner. The rear mold is in the bone position and the pillow position.
Drilling, pinholes, and ejector pins; mold ejector pin holes, waterway hole processing positions, and position pressing; drilling, pinholes, and ejector pins
Flat top, compound thimble, and matching thimble; Inclined top.
There is a requirement for a high level of processing accuracy. A zinc alloy die-casting mold is typically made up of three distinct mold components: a concave mold, a punch mold, and a mold base. It's possible that some of them are multi-piece modules. Therefore, high levels of processing accuracy are required for the combination of upper and lower molds, the combination of inserts and cavities, and the joining together of modules. Precision molds typically achieve a level of dimensional accuracy that is measured in micrometers.
Some products with complicated shapes and surfaces, such as automobile panels, aircraft parts, toys, and home appliances, have a surface that is composed of a number of different curved surfaces in varying degrees of curvature. As a result, the cavity surface of the die-casting mold for zinc alloy is extremely complicated. Mathematical analysis is required for the treatment of some surfaces. The production of molds in small batches is not the same as production in mass quantities, and in many instances, only a single batch is made.
The production of multi-process molds always employs a variety of processes, including milling, boring, drilling, reaming, and tapping, among others. There is a finite amount of time that can be spent using molds for repetitive production. Because a mold needs to be replaced with a new one when it reaches the end of its service life, the production of molds is frequently iterative. In the production of molds using profiling processing, there are times when neither drawings nor data are available. In these cases, the profiling processing has to be carried out based on the actual object. For this purpose, high imitation accuracy die casting products and the absence of deformation are required.
The materials used to make molds are of superior quality and have a high degree of tenacity. The high-quality alloy steel is typically used in the construction of molds as the primary material. Ledeburite steels, such as Crl2 and CrWMn, are frequently used in CNC machining the production of molds, particularly those with a long service life. When it comes to blank forging, processing, and heat treatment, this particular type of steel has very specific requirements. As a result, one cannot ignore the preparation of the processing technology, and heat treatment deformation is also a problem that needs to be taken seriously during the processing stage.
Prior to semi-finishing, the side datum plane is aligned to ensure accuracy; semi-finishing 2D and 3D profiles, and finishing various installation working surfaces (including limit block mounting surface and contact surface, insert mounting surface and backrest surface, punching surface), Head mounting surface, waste cutter mounting surface and backrest surface, spring mounting surface and contact surface, various stroke limit working surfaces, wedge mounting surface and baComplete the height reference surface as well as the process reference hole, and then record the data.
Before finishing, alignment of the process reference hole datum plane and insert allowance inspection; finishing profile 2D, 3D, side punching profile and hole location; finishing process reference hole and Height reference; finishing guide surface and guide hole. Inspection and review of the machining accuracy, bench work, and inlay process. The process should be prepared succinctly and expressed in detail, and the processing content should be expressed numerically as much as possible; the process should place particular emphasis on key and difficult processing points; the process should be clearly expressed where combined processing is required; when the insert needs to be processed separately, attention should be paid to the process requirements for processing accuracy; and the process should be carried out in the following order: 1. mix and match. After processing, for the insert parts that need to be processed separately, the process installation is the benchmark requirement for separate processing while combined processing is taking place; springs are the most easily damaged in zinc alloy die-casting mold processing, so mold springs with a long fatigue life should be selected.