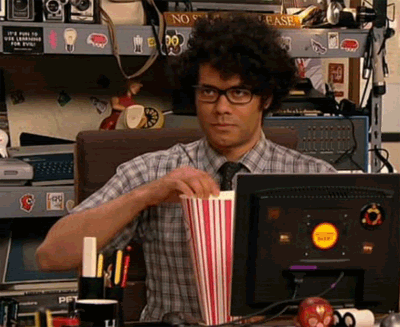
Announcement
Collapse
No announcement yet.
New DS3 Intercooler from Alive Tuning - stay tuned (pun intended)
Collapse
X
-
Originally posted by Dangerousfish View PostPerformance Powered By Thought
Engineered Horsepower
Comment
-
Originally posted by Czar View PostLMAO, I thought I could relatively easily condense an article I wrote on Water/Methanol injection quite a few years ago, seems I'm simply rewriting the whole article again, including the technical science behind the two liquids, please be patient with me, this may take me a little while, I also think it might be best in a separate thread.cyclone> Fish is the man
Comment
-
Originally posted by Dangerousfish View Post
I've taken out all the mathematical science, lots of my original article, and simplified the best I can, just to get the ball rolling, I hope this helps.
The principles of spraying (injecting) 100 % water through nozzles (jets) of various sizes pumped under pressure to cool the intakes charged air, is an efficient way to remove heat from the intakes charged air, only to the point where the evaporation of the injected water is effective, the hotter the charged air, the greater the cooling efficiency from the injected water, we can further enhance the cooling effect, with the introduction of Methanol (Alcohol) with a variation % mix with water all the way to a 100% Methanol content.
The addition of Methanol has two benefits, not only does it enhance the cooling effect of the intakes charged air, taking over from where the water evaporation cooling looses efficiency, it can also add power, Methanol carries an oxygen atom, don't get over excited on the later, there's more to it than what you may think !!
We all get the above, right, good, let's move on, I'm trying my best to keep the mathematical science out of this, well, for now, we may have to include it, if and as questions are raised on this subject.
Cooling the intake air charge.
Ambient Air enters the turbo intake, this air is compressed generating heat, the compressed air is subject to the heat soak from the hot side of the turbo to the cold compressor side, the air exiting the turbo is in the region of 90°-150°c generally this hot air passes through an intercooler, how much heat dissipates, depends on the intercoolers efficiency, and not just on the volumetric size. !!!
This post intercooler intake charged air tubing is where most installations of WMI (water/Methanol injection) nozzles (jets) are placed, prior to the TP (temperature/pressure) sensor, injecting after this, changes the rules again, more on this if,as or when needed.
If we have an efficient intercooler do we need and does WMI still have cooling benefit, keeping it simple for now, the cooler the intake air charge exiting the efficient intercooler, the less efficiency from the WMI system, that said, this is where Methanol comes in to its own, as the intake charge air will generally be around 50°c and heat removal from water evaporation has lost efficiency, Methanol continues to remove heat more efficiently than water at these sub boiling point pressurised temperatures.
So why not inject 100% Methanol, Methanol has a lower boiling point than water, and has not the energy molecular mass to dissipate heat per volume over water.
Can we inject pre turbo, yes we can, albeit at the expense of compressor wheel degradation.
How about injecting post turbo pre intercooler, that would render your intercooler useless, why bother having one.
Could we spray the outside of the intercooler to keep that cool, yes we can and there are kits to do just this.
What about spraying post TP sensor, this is a whole different league, if you really want to do this, then we can look at this as we get more in depth.
How do I % mix water and Methanol, it is accurately mixed by weight, NOT by volume.
Costs: a decent kit £500.00 +
Replenishment of A grade Oxygenated Methanol
Upgrading to Stainless steel tubing/lines and seals to withstand the greater the % Methanol content, as it is highly corrosive.Performance Powered By Thought
Engineered Horsepower
Comment
-
Originally posted by Superfly Guy View PostGreat piece, im assuming the volume injected is regulated relevant to the air temps at some point in the loop.Performance Powered By Thought
Engineered Horsepower
Comment
-
Nice summary Czar, thanks.
Another point on WMI, Ragnarok, if i remember correctly, seemed pretty sure that his WMI system was preventing the dreaded carbon buildup on the inlet valves... makes sense in theory too. There are some details in his build thread I think...
Comment
-
Originally posted by tch View PostNice summary Czar, thanks.
Another point on WMI, Ragnarok, if i remember correctly, seemed pretty sure that his WMI system was preventing the dreaded carbon buildup on the inlet valves... makes sense in theory too. There are some details in his build thread I think...
As I am sure most of you who have any interest with the understanding how we keep inlet valves clean in a IC (internal combustion) engine, will know the difference between a wet and dry intake manifold tract, that's right, wet = continuous fuel wash. dry = no fuel wash whatsoever, and of course all GDI engines are indeed dry tract systems, hence the excessive and rapid carbonisation on the inlet valves.
WMI is not a continuous running system with the running of the engine, and in most cases, the cc's or ml/min injected into the intake air system is not sufficient for the benefit of fuel wash, having said that, don't dismiss the theory just yet, this is where it gets a little interesting, as we have already touched upon, the injected solution, evaporates in the hot intake air system removing heat, however, not all of the injected solution will evaporate, what doesn't evaporate, will wash over the inlet valves, now, just how much of the original injected amount cc's or ml/min is dependant on nozzle/s (jets/) location, boost pressure in this case, heat evaporation and droplet size injected, i use the word wash quite lightly here, as what you have to be aware of is, although your monitoring device/s may read a charge air temperature of, for arguments sake, let's say a few degrees above ambient, this temperature registered by the TP (temperature/pressure) sensor, is not what enters your engine combustion chamber.
During the non evaporated solutions journey into the cylinder head intake runner tracts, providing any remaining solution gets this far, is then subject to the very high temperatures deep within the intake tracts just at the very backs of the inlet valves, where the carbon build is, and this is formed due to the very high temperatures solidifying any suspended oil particles from the internal routed venting of the crankcase gases, during the power and exhaust stroke cycles, we have valve overlap and reversion take place, this is where we have the combustion flame exiting the exhaust valve on the exhaust stroke cycle, yet as the exhaust valve/s begin to close, we also start to open the inlet valve/s at the same time, this is valve overlap, you now are subjecting the inlet valve/s to the combustion chamber combustion heat, don't get me wrong, the faces of the inlet valves are always subject to the combustion heat, what's happening during valve overlap is reversion, where the exiting combustion pressure is greater than the incoming charged air, and so some of the combustion flame tries to exit the combustion chamber via the inlet valve/s, we try to minimise and prevent the valve/s overlap with complex timing control.
With that out of the way and understood, any remaining solution that gets to the inlet valve/s very very very quickly becomes super heated steam, and it is this extreme super heated steam, which can help with the control of carbonisation of the inlet valves, that said, if you already have excessive carbon build up on your inlet valves, injecting a W/M solution will not wash away your carbon, unless you inject the solution on a continuous cycle, directly into the intake manifold tracts, if you have a fresh set to cleaned inlet valves, again, dependant on the answer above, will depend on the future carbonisation of your inlet valves.Performance Powered By Thought
Engineered Horsepower
Comment
-
Great write up as usual Czar.
If I've understood correctly, it wouldn't be recommended to install a WMI system on a server that's already suffering excessive carbonisation due to the increased heat this can generate during combustion over a smaller surface area? Or is this still likely to provide the valves with a light rinse in a positive way?cyclone> Fish is the man
Comment
-
Originally posted by Czar View PostHaving written about WMI and the excessive carbonisation of the inlet valves on GDI engines, on this forum and countless forums worldwide, along with PM's and email Q & A's for more years than I care to remember, the theory and my answer to this remains the same.
As I am sure most of you who have any interest with the understanding how we keep inlet valves clean in a IC (internal combustion) engine, will know the difference between a wet and dry intake manifold tract, that's right, wet = continuous fuel wash. dry = no fuel wash whatsoever, and of course all GDI engines are indeed dry tract systems, hence the excessive and rapid carbonisation on the inlet valves.
WMI is not a continuous running system with the running of the engine, and in most cases, the cc's or ml/min injected into the intake air system is not sufficient for the benefit of fuel wash, having said that, don't dismiss the theory just yet, this is where it gets a little interesting, as we have already touched upon, the injected solution, evaporates in the hot intake air system removing heat, however, not all of the injected solution will evaporate, what doesn't evaporate, will wash over the inlet valves, now, just how much of the original injected amount cc's or ml/min is dependant on nozzle/s (jets/) location, boost pressure in this case, heat evaporation and droplet size injected, i use the word wash quite lightly here, as what you have to be aware of is, although your monitoring device/s may read a charge air temperature of, for arguments sake, let's say a few degrees above ambient, this temperature registered by the TP (temperature/pressure) sensor, is not what enters your engine combustion chamber.
During the non evaporated solutions journey into the cylinder head intake runner tracts, providing any remaining solution gets this far, is then subject to the very high temperatures deep within the intake tracts just at the very backs of the inlet valves, where the carbon build is, and this is formed due to the very high temperatures solidifying any suspended oil particles from the internal routed venting of the crankcase gases, during the power and exhaust stroke cycles, we have valve overlap and reversion take place, this is where we have the combustion flame exiting the exhaust valve on the exhaust stroke cycle, yet as the exhaust valve/s begin to close, we also start to open the inlet valve/s at the same time, this is valve overlap, you now are subjecting the inlet valve/s to the combustion chamber combustion heat, don't get me wrong, the faces of the inlet valves are always subject to the combustion heat, what's happening during valve overlap is reversion, where the exiting combustion pressure is greater than the incoming charged air, and so some of the combustion flame tries to exit the combustion chamber via the inlet valve/s, we try to minimise and prevent the valve/s overlap with complex timing control.
With that out of the way and understood, any remaining solution that gets to the inlet valve/s very very very quickly becomes super heated steam, and it is this extreme super heated steam, which can help with the control of carbonisation of the inlet valves, that said, if you already have excessive carbon build up on your inlet valves, injecting a W/M solution will not wash away your carbon, unless you inject the solution on a continuous cycle, directly into the intake manifold tracts, if you have a fresh set to cleaned inlet valves, again, dependant on the answer above, will depend on the future carbonisation of your inlet valves.
In the ECU update files, they rewrite the complex vanos camshaft timing phase, this further reduces the already very tiny window of valve overlap and reversion, and so now hopefully you will understand, that a what may seem a pointless ECU update, has a relevant bearing on the actual effects of carbonisation, due to adjusting when and how long the valves open and close, this further effects combustion pressures, and of course, the initial crankcase windage, from combustion pressure blow by past the piston rings, you see it's all relevant, so Citroen really are trying to help.
Originally posted by Superfly Guy View PostI've just read that on my phone whilst bouncing around on a train, my eyeballs are aching.
Originally posted by Dangerousfish View PostGreat write up as usual Czar.
If I've understood correctly, it wouldn't be recommended to install a WMI system on a server that's already suffering excessive carbonisation due to the increased heat this can generate during combustion over a smaller surface area? Or is this still likely to provide the valves with a light rinse in a positive way?Performance Powered By Thought
Engineered Horsepower
Comment
-
Valve overlap is very similar to egr in a way, the mixing of spent exhaust gases recirculated back into the combustion mix. Helps reduce Nox emissions and cool down combustion temps and stratisfied combustion modes. It can also increase volumetric efficiency above 100% in a naturally aspirated engine. Reducing overlap in a boosted engine will help with spooling the turbo. Have ours reaching peak boost below 3000rpm instead of 4200rpm by reducing overlap in these load areas.
I've never seen any changes to reduce overlap on the camshaft timing on sw updates for the DS3. In fact the most recent update(5FV engine) just richens the mixture, small changes to ignition advance, decreases the boost,makes knock detection less sensitive and knock correction less aggressive. Oh and some changes to the DTC tables.
To be fair the best update they've done....runs so much better.
I'll post up cam timing map where you can see how much advance the intake cam runs.
White on red THP
Miltek exhaust with HKS highflow cat, Forge intercooler, hard pipe kit, induction kit, oil catch tank, , VAG BOV, Stage 3 SPT remap 217 BHP
Comment
-
Very interesting read. What kind of consumption rates does the WMI system have in terms of the methanol?
Just thinking of potential health risks given that MeOH is a carcinogen, and quite a volatile one. I would assume it all gets fully combusted once injected, as it burns very efficiently so there's no unburnt MeOH to worry about, but what kind of storage tank does it use, where is it located, are leaks a possibility, and would there be exposure risks from refilling? (depending on how much it needs, see my question about consumption rates)
To be honest, I'd be happy to read the whole paper - I studied chemical engineering so this sounds right up my alley
Comment
-
Originally posted by BenS View PostVery interesting read. What kind of consumption rates does the WMI system have in terms of the methanol?
Just thinking of potential health risks given that MeOH is a carcinogen, and quite a volatile one. I would assume it all gets fully combusted once injected, as it burns very efficiently so there's no unburnt MeOH to worry about, but what kind of storage tank does it use, where is it located, are leaks a possibility, and would there be exposure risks from refilling? (depending on how much it needs, see my question about consumption rates)
To be honest, I'd be happy to read the whole paper - I studied chemical engineering so this sounds right up my alleyLA PETITE FUSEE / THE LITTLE ROCKET
sigpic
Comment
-
Get me some crude oil and I'll make us some petrol/diesel for cheap rates aye? :P
Comment
Comment